Why High Price For High-quality LED Products? Part – 5
After analyzing LED lead frames and chips in terms of their qualities and costs, this time we will talk about another component in all LED products—the encapsulant.
LED packaging encapsulant
As we know, the chip is the core component of an LED emitter. In order to ensure the chip’s stable performance, the packaging encapsulant acts as a key role within. The function of packaging encapsulant mainly consists of three aspects: (1) Sealing. The encapsulant prevents water, sulfur and other elements from penetrating into the LED, blocking moisture as well as dust. (2) Immobilization. It mechanically fixates the wires which connect the chip and the frame, thus preventing vibration of the wires. (3) Light extraction efficiency. The high refractive index of the encapsulant is favorable for decreasing light loss resulted from boundary reflection. Besides, it evenly mixes the phosphors to generate white light with blue chips and helps expand color diversity of the LEDs.
Types of encapsulants
In general, most LED packaging companies utilize epoxy resin, methyl silicone resin and phenyl silicone resin to encapsulate LEDs. The table below shows the comparison among these three types of encapsulants in five dimensions.

The advantages of epoxy include high sealability, high shock resistance, excellent protection performance and low cost. While it also has flaws, for instance, the weakness in heat and weather resistance, high possibility to crack and yellow, and so on. Therefore, except for low-end market, there are almost no LEDs packaged in epoxy resin now.
Compared with epoxy resin, silicone resin shows some excellent merits, such as good UV prevention, high heat resistance and good heat dissipation performance. With the development of LED industry, low power LEDs cannot meet the market’s needs for brightness anymore, which means medium and high power LEDs will become increasingly popular in the near future. When being applied, medium and high power LEDs generate much more heat than low power ones. That’s why the packaging encapsulant must be more reliable in terms of heat resistance and heat dissipation performance.
Silicone resins, according to their chemical structures, can be divided into two types: methyl silicone resin and phenyl silicone resin. Both of them have their own pros and cons. For example, methyl silicone resin has better UV resistance, thus it is widely adopted for violet-chip LEDs to promote products’ reliability. And the latter is better than the former in refractive index. That is why most medium and high power LEDs adopt phenyl silicone resin for improvement of light efficiency.
Effects of encapsulants’ quality on LEDs
There are two sides to every coin. Both epoxy resin and silicone resin can bring positive effects to LEDs, while there are also side effects due to their physical properties. Therefore, a superior LED packaging encapsulant must overcome the drawbacks. The primary function of packaging encapsulant is providing a well-sealed, safe and reliable environment for the chip to work. Now, we will explain the influences on packaged LEDs caused by the physical properties of the encapsulant.
1. Sealability
The major function of packaging encapsulant is to create a totally sealed working circumstance for LED chips, in case that water, sulfur or other elements penetrate into LEDs and result in malfunction. Different from tungsten, the beam angle of LED chips is around 120°. Yet the light coming out from the chip get reflected, most of which cast back onto the frame. To offset such a loss in light efficacy, the surface of the frame is always coated with a layer of silver to reflect the light again. If the sealability of the encapsulant is imperfect, the sulfur in the air will penetrate into the LEDs and react with the silver. As a consequence, the reaction product– silver sulfide is formed and the light efficacy is largely compromised. Figure 1 below shows the process of sulfidation where the color of function area gradually changes from silver to black.
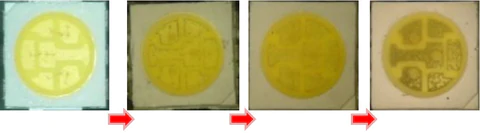
Apart from this, bad sealability may also bring about the penetration of other organic compounds. Any kind of volatile compounds are likely to permeate into the porous structured organic silicone and occupy the gaps among the molecules. When being heated, the compounds will change in color and absorb light selectively. As a result, the overall performance of LEDs, including luminous flux, light efficacy, and color temperature reliability, will be influenced.
2. Heat and moisture resistance
When an LED is working, it generates vast amount of heat especially for most white light LEDs. Even though there are some heat management solutions, including lead frames that conduct the heat out, there are still heat inside generated by the phosphor. Bad heat dissipation of the encapsulant keeps the heat within and creates a high temperature environment. After long hours of work, the heating problem could easily lead to crack and carbonization of the encapsulant, which can cause performance degradation and eventually luminous decay. More seriously, the crack can break the conduct wires apart and lead to LED failures.
As for moisture resistance, it shows the encapsulant’s ability to keep the moisture outside the LED. As mentioned before, bad heat resistance generates cracks in the encapsulant, leading to moisture penetration and failure of the LEDs. Furthermore, the encapsulant has its own property that takes up and retain the moisture in the air. Consequently, the moisture expansion and atomization will occur and impact LEDs function. So, the resistance abilities of heat and moisture of the encapsulant are crucial to an LED’s performance and quality. Figure 2 shows the atomization of an LED due to moisture penetration.
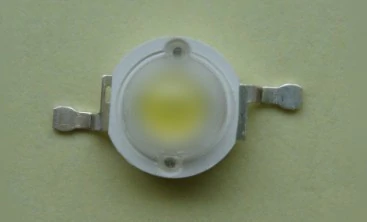
Yuji High CRI LEDs with superior packaging encapsulant
In terms of cost, the encapsulant takes up a small but non-negligible portion. A high-end packaging encapsulant of a well-known brand is about 450 USD/kg, while you can also get one kilogram of low-end encapsulant for ten bucks on the market with uncertain quality. We can take SMD 2835 for instance, which is the most typical 0.2 watt SMD on the market. According to the statistics from LEDinside, in August 2016, the average price of SMD 2835 is 7 USD and the lowest 4 USD. Assume that 1000 pieces of SMD 2835 need 5g packaging encapsulant, then the cost of high quality encapsulant will be more than 2.25 USD. However, by contrast, the cost of low quality encapsulant can be negligible.
Yuji LED aims to provide high quality high CRI LEDs. To keep the CRI value over 95, mixture of blue or violet chip and phosphor are used. Compared to LEDs with lower CRI, high CRI LEDs will compromise a part of luminous efficacy and generate more heat. Therefore, when developing high CRI LEDs, Yuji applies packaging encapsulants from well-known manufactures to meet the demand for heat resistance. In order to evaluate the products’ reliability, we conduct LM80 aging test on all our products. This test is done at temperatures of 55℃,85℃and 105℃ and humidity within 45%-65%, with the LEDs on for 10,000 hours successively. Figure 3 below is the LM80 test result of Yuji SMD 2835.
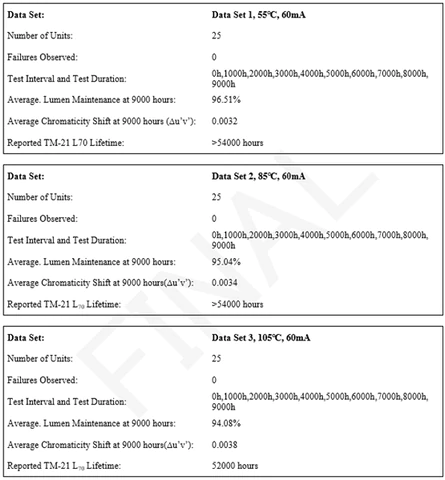
The result shows that the lifespan of an LED is impacted by external temprature. After 10,000 testing hours, the luminous attenuation is 3.5% at 55℃. While at 105℃, it only increases 2.5% to a 6% decay. Even at a temperature as high as 105℃, the estimated average lifespan of Yuji LEDs reaches 52,000 hours, which far exceeds the industry standard—30,000 to 50,000 hours.
After long term use, the light color will inevitably change due to phosphor attenuation, and this change can be measured by chormaticity coordinates shift. Yuji packaged LEDs have the shift about just 0.0032 to 0.0038 even after 10,000 hours, standing out in the industry.
Conclusion
Lead frames, chips and encapsulants are all key components of packaged LEDs. Any breakdown of these parts will lead to overall degradation of the LED’s performance and will eventually compromise user experience. Hence, we must choose high quality packaged LEDs when producing light fixtures.